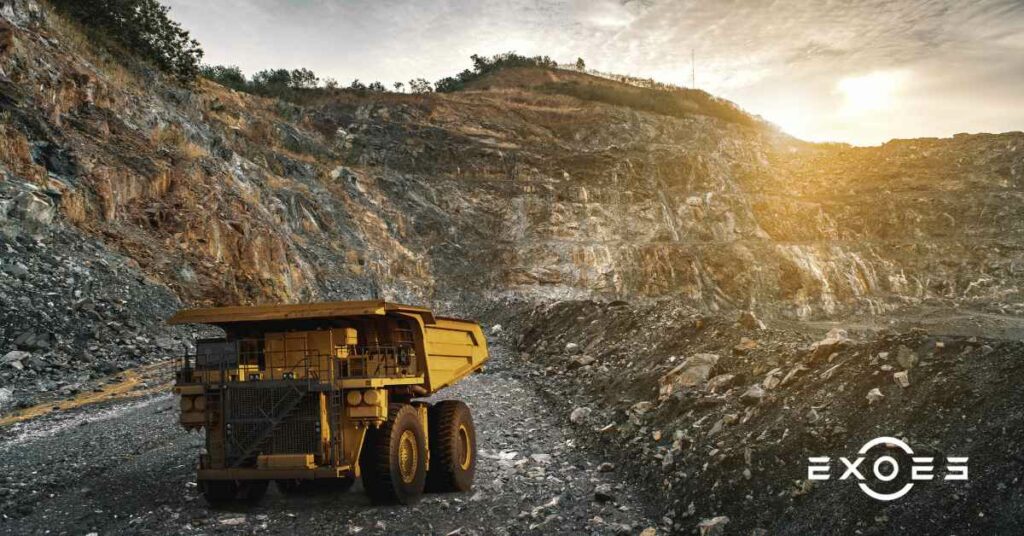
Au cours des dernières années, l’industrie minière a été confrontée à une pression croissante pour réduire son impact environnemental et adopter des pratiques durables.
« Les industries extractives sont responsables de la moitié des émissions mondiales de carbone et de plus de 80% de la perte de biodiversité ».
« Resource extraction responsible for half world’s carbon emissions », The Guardian, 2019
Alors que les gouvernements et les organismes de réglementation se concentrent sur la réduction des émissions des moteurs des véhicles NRMM (Non-Road Mobile Machinery), le secteur minier se trouve à un carrefour critique.
La mise en œuvre de la réglementation sur les NRMM, qui fixe des limites d’émissions pour les moteurs des NRMM en fonction de leurs gammes de puissance et de leurs applications, remodèle le paysage de l’industrie et entraîne la nécessité de systèmes de propulsion alternatifs.
Malgré la reconnaissance des avantages de l’électrification par l’industrie, la transition a été plus lente par rapport à d’autres secteurs.
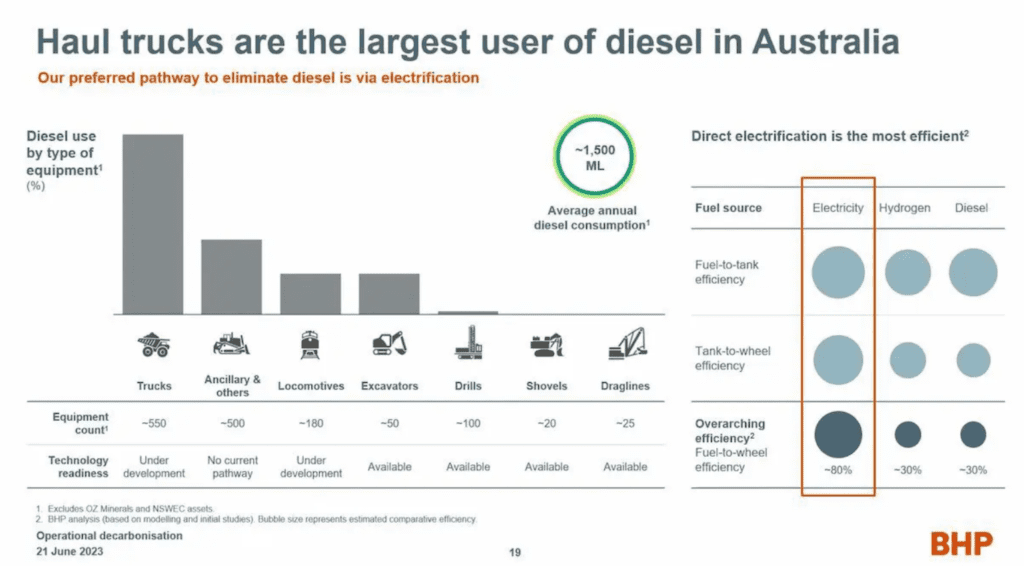
Pourquoi l’électrification de l’industrie minière est-elle si complexe ?
Les entreprises minières cherchent à réduire leur empreinte carbone et à adopter des pratiques durables.
Cependant, plusieurs facteurs critiques contribuent à la complexité de cette transformation : la variation extrême des températures, les exigences en matière de capacité de stockage d’énergie et le besoin d’une infrastructure de recharge adéquate.
Les enjeux de l’électrification sont pourtant bien présents quand on sait que 30% des dépenses d’une entreprise minière sont liées à la consommation de diesel.
Les variations de températures
Les opérations minières se déroulent souvent dans des environnements divers et exigeants, soumettant les équipements à des températures extrêmes et à des conditions difficiles.
Des climats glaciaux aux chaleurs écrasantes, les variations peuvent poser d’importants défis pour les véhicules miniers électriques.
Les batteries, composants cruciaux des véhicules électriques, peuvent subir une diminution des performances et de l’efficacité en cas de températures extrêmes. Assurer le fonctionnement fiable et optimal des batteries dans de telles conditions exige le développement de technologies de batterie spécialisées et de systèmes de gestion thermique.
Le besoin d’une forte capacité de stockage d’énergie
Les véhicules miniers sont généralement des machines robustes conçues pour fonctionner dans des conditions difficiles, nécessitant une puissance et une énergie considérables.
Pour égaler les performances et l’endurance de leurs homologues fonctionnant au diesel, les véhicules miniers électriques nécessitent une certaine capacité de stockage d’énergie.
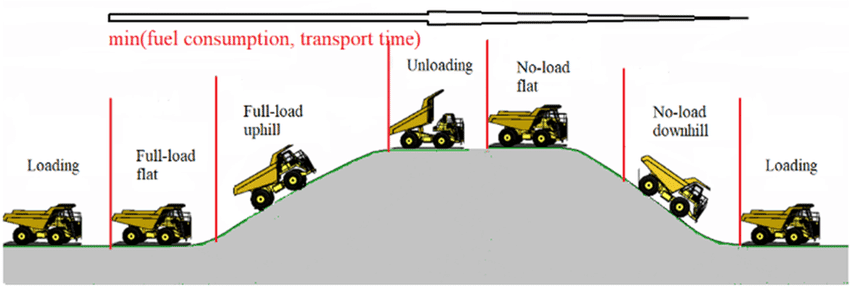
Un cycle de transport exigeant. Source : Implementation of velocity optimization strategy based on preview road information to trade off transport time and fuel consumption, Research Gate
Cela requiert des technologies de batteries avancées capables de stocker et de fournir suffisamment d’énergie pendant des périodes prolongées sans compromettre les performances du véhicule.
Améliorer la densité énergétique, la durabilité et l’efficacité globale de la batterie devient impératif pour répondre aux exigences exigeantes des opérations minières.
Le besoin d’une infrastructure de recharge spécifique
Une infrastructure de recharge efficace et fiable est essentielle pour l’adoption généralisée des véhicules miniers électriques. Cependant, établir un réseau de recharge complet dans des sites miniers éloignés peut représenter un défi logistique.
La nécessité d’une infrastructure de recharge robuste capable de répondre aux demandes élevées en puissance des véhicules miniers est donc essentielle.
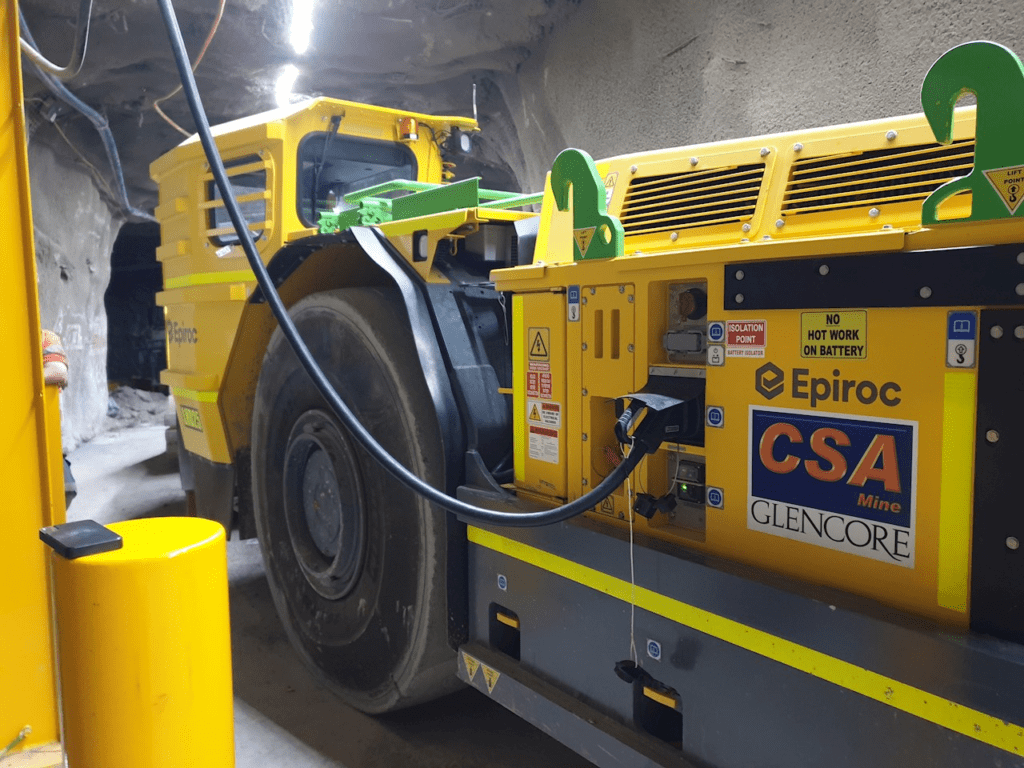
Source: ABB develops Australian first for electric charging at CSA copper mine, ABB, 2022
De plus, le processus de recharge doit être optimisé pour réduire au minimum les temps d’arrêt, car les opérations minières fonctionnent souvent selon des horaires serrés. Le développement de solutions telles que les technologies de recharge rapide, les stations de recharge décentralisées et l’intégration intelligente au réseau électrique sont cruciaux pour assurer la praticité et la viabilité de l’électrification de l’industrie minière.
Gestion thermique par immersion : une solution à ces défis ?
Alors que l’industrie minière est confrontée aux défis de l’électrification, des solutions innovantes émergent pour surmonter les obstacles spécifiques liés aux variations de température, aux exigences de capacité de stockage d’énergie et à l’infrastructure de recharge.
Une solution qui présente une immense promesse est la gestion thermique par immersion (ou immersion cooling thermal management). Voilà pourquoi.
l’immersion permet une résistance aux variations extrêmes de température
L’une des principales préoccupations dans les opérations minières est la capacité des batteries à résister aux variations extrêmes de température. La gestion thermique par immersion offre une solution efficace en submergeant les modules de batterie dans un fluide diélectrique thermiquement conducteur.
Cette approche offre une régulation de température supérieure, garantissant que les batteries restent dans la plage de fonctionnement optimale même dans des conditions environnementales difficiles. En maintenant une température constante, la gestion thermique par immersion atténue le risque de dégradation des performances et prolonge la durée de vie de la batterie, améliorant ainsi la fiabilité et l’efficacité des véhicules miniers électriques.
L’immersion pour une recharge ultra rapide
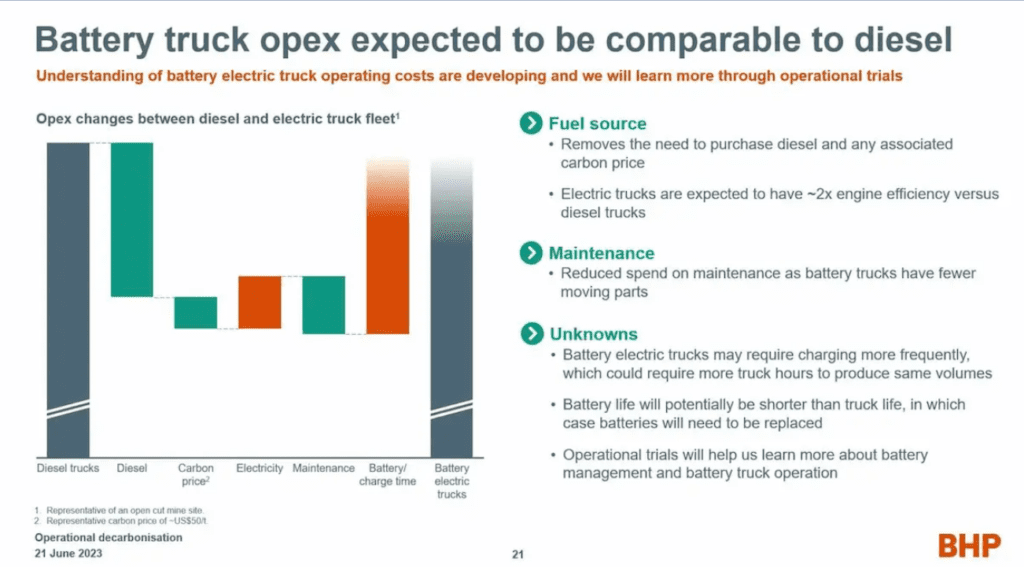
En immergeant les modules de batterie dans un fluide thermiquement conducteur, la chaleur générée pendant le processus de recharge est dissipée extrêmement efficacement par rapport aux systèmes traditionnels refroidis par air (air cooling).
Cette efficacité de refroidissement améliorée permet des taux de recharge plus élevés sans compromettre l’intégrité de la batterie. En conséquence, les exploitants miniers peuvent réduire considérablement le temps de recharge, ce qui permet une utilisation accrue des véhicules et une optimisation de l’efficacité opérationnelle.
Sécurité, résistance et durée de vie prolongées
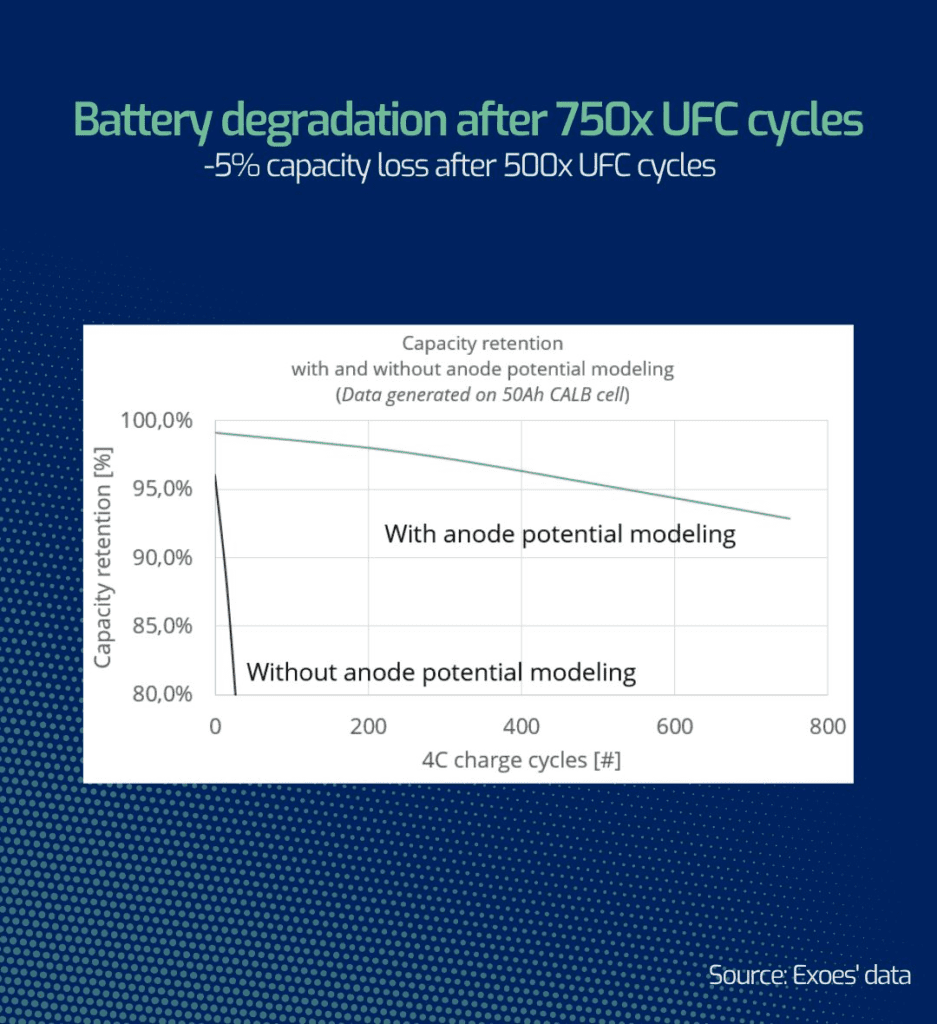
Le fluide diélectrique utilisé dans les systèmes de refroidissement par immersion agit également comme une barrière de protection, protégeant les modules de batterie contre les éléments externes tels que la poussière, l’humidité et les vibrations.
Cette protection supplémentaire améliore la durabilité et la longévité des batteries, réduisant les besoins en maintenance et les coûts opérationnels globaux. De plus, la gestion thermique par immersion élimine le besoin de systèmes de refroidissement par air complexes, simplifiant la conception et réduisant le poids et l’encombrement du système de gestion thermique dans les véhicules miniers.
Pour en découvrir davantage sur la technologie de refroidissement par immersion, découvrez le replay de notre dernier webinaire :
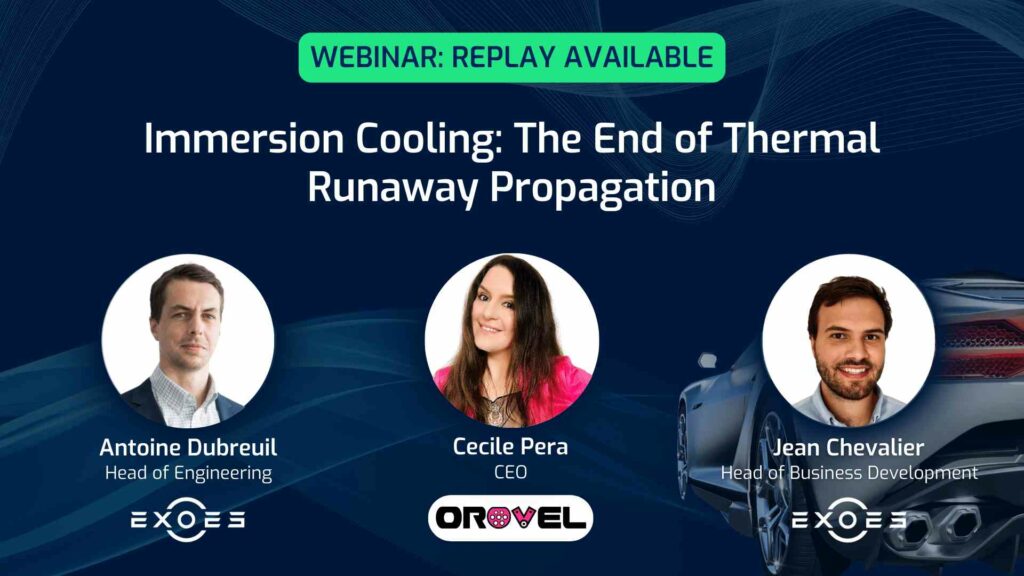